With 26 manual pack stations, BAX Music’s main objective was to reduce costs, especially labor costs – one of the key benefits of automation.
We support your stage.
BAX Music was started in 1998, by two brothers who had shared a passion for music since their teenage years. Originally renting DJ and gig support equipment, the company grew fast and began selling equipment on the internet in 2005. After expanding into instrument sales in 2010, BAX Music now offers more than 48,000 items, meeting a huge range of needs for both amateur and professional DJs and musicians. Today, 450 employees ship a million packages to customers every year, all supported by the same passion for music.
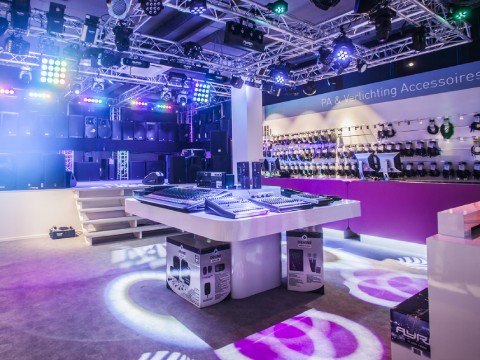
Customer needs
Reducing costs
Cutting temporary worker numbers
BAX Music often needed temporary workers to meet demand, especially during peak periods (May and year-end) when 80 temps could be required. Hiring such large numbers was not a trivial challenge.
Enhancing the customer experience
BAX Music wanted to use automation to limit human error and improve the customer experience. Maintaining very high customer satisfaction is a key focus for the firm.
Coping with business growth
BAX Music continues to see strong growth (more than 100,000 customers last year), resulting in high demand. They needed to increase their productivity so they could cope with orders and ensure that customers were not kept waiting.
Our solutions
Following analysis and discussion, Ranpak and BAX Music teams agreed that the Cut’it! EVO and Lid’it! machines provided the right solution for BAX Music’s needs. The Machines formed part of a larger automation investment plan, with an expected return on investment of 3 years.
BAX Music’s growth rate made automation essential, in order to cope with increased activity. The company also has 25 different carton sizes, so two Cut’it! EVO machines are used (one M version and one L version), along with a Lid’it! machine for letterbox-size packages. Cut’it! EVO detects package height and automatically adjusts boxes to the highest point of filling. This reduces package size and minimizes voids. A glued lid is then applied onto the now smaller carton. Lid’it! is used to close smaller-height boxes suitable for letter-boxes. The entire installation process was supported by Ranpak’s engineers, with close collaboration with BAX Music teams and trouble-free results.
Business results
Reduced costs
The main objective was to reduce costs, especially labor costs resulting from the use of temporary workers. Approximately 80 temps used by BAX Music before process automation have now fallen to just 25. Employees are also now able to focus on more productive tasks, resulting in cost savings even higher than originally anticipated.
Increased productivity
79% of total package volume is now packed using automated solutions. The firm doubled productivity within its outbound process, rising from 7.5 orders per hour for each operator to 15-16 orders.
Improved customer experience
Before automation, each package had to be processed manually. Choosing a suitable carton from 25 different sizes was complex, and mistake could happen. Now BAX Music no longer has to worry about picking the right carton, because the choice is made automatically by the Cut’it! EVO machine. The result is fewer mistakes seen by customers, and even better customer experience.
We’re here for you
Contact a Ranpak Specialist to find the right solution for your company, products and industry.
IMPORTANT - You are Now Leaving this Website
You are now leaving the Ranpak website. The website you will be entering is not owned or operated by Ranpak and/or its subsidiaries. The content, products and information contained on third party websites are not owned or controlled by Ranpak and/or any of its subsidiaries. Therefore, Ranpak makes no representations about, does not endorse or adopt, and is not responsible or liable for damages relating to the third party, its products or services, its website, its privacy policies or practices, or the content of the third party website.