Helly Hansen aimed to reduce packaging waste and improve package size. Making sustainability an active part of their operation and customer-facing experience reinforces their brand values and also aligns with the values of their customers.
Automated packaging solutions triple throughput for global outdoor apparel leader
Helly Hansen sells its own skiing, sailing, workwear, and outdoor clothing in more than 40 countries. Since 1877, the company has expanded its range of high-quality products, starting with one of its first major innovations: the first-ever supple waterproof fabrics. Alongside a reputation for quality, Helly Hansen is known for its commitment to sustainability.
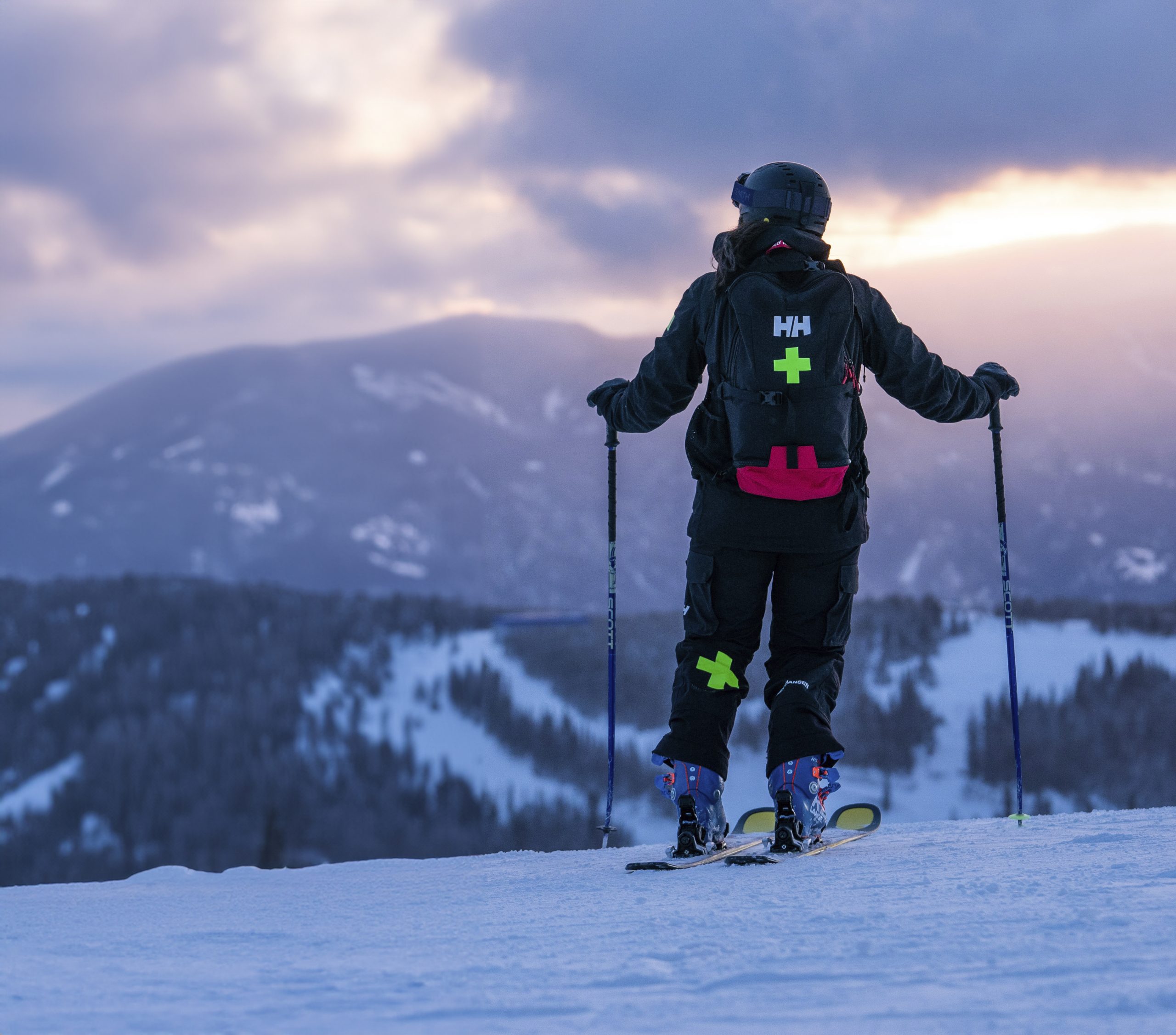
Customer needs
Sustainability
Cost efficiency and capacity
Helly Hansen’s packing operation was labor intensive. Package data entry for logistics providers was sent to carriers based on standard and theoretical data out of their warehouse management system (WMS). Theoretical data introduced errors, which slowed the invoice verification process. Helly Hansen also faced package theft issues due to poor quality of taped boxes.
Improved unboxing experience
Helly Hansen aimed to enhance the customer’s unboxing experience by addressing several factors: a box that isn’t too large, materials that are clearly more sustainable and easily recyclable, and packaging that is more tamper-resistant yet still easy for customers to open.
Our solution
Ranpak conducted an analytical review of existing and future requirements for Helly Hansen’s packaging strategy. Ultimately, Ranpak recommended replacing their existing manual packing setup with an automated end-of-line (EOL) configuration. Automated packaging machines would lead to improved throughput and scale seasonally while optimizing staff productivity.
Ranpak recommended two types of machines to boost both efficiency and sustainability: a Form’it!™ Case box erector and a Cut’it!™ EVO right-sizing machine.
The Form’it! Case streamlines case erection by creating up to 15 boxes per minute, while the Cut’it! EVO machine automatically shortens cartons to match their highest point of filling before gluing a tamper-evident lid in place. This combination results in a no-waste approach, with significantly smaller voids in parcels before shipping and minimized shipping costs.
Business results
Reduced labor costs
The Helly Hansen operation is now more efficient and packing line staff are working at more ergonomic stations, which improves their overall well-being.
Tripled throughput
Following a successful implementation during a season of record sales, throughput tripled from 300-400 boxes per hour up to 1,000 boxes per hour.
Better data visibility
Automation improved real-time data integrity and accessibility, with accurate measurements and weights available to share with carriers. This facilitates carrier invoice verification while ensuring accuracy.
Loss prevention
Tamper-evident lids keep opportunities for theft during transit to a minimum. Removing tape as the primary box sealant has resolved a big part of the theft-in-transit problem.
Looking for ways to optimize your operation? Talk to our experts
Whether just beginning your automation journey or adding new capabilities to a brownfield site, Ranpak’s team is ready to identify the ideal solutions for you. Get in touch now to start a conversation that will lead to improved productivity, material efficiency, and unrivaled ROI.
Let’s start the conversation
IMPORTANT - You are Now Leaving this Website
You are now leaving the Ranpak website. The website you will be entering is not owned or operated by Ranpak and/or its subsidiaries. The content, products and information contained on third party websites are not owned or controlled by Ranpak and/or any of its subsidiaries. Therefore, Ranpak makes no representations about, does not endorse or adopt, and is not responsible or liable for damages relating to the third party, its products or services, its website, its privacy policies or practices, or the content of the third party website.